
Introduction
Manufacturers of sustainable clothes and footwear typically follow one of three paths to minimizing the environmental cost of their products.
The first is to manufacture goods created from natural materials that can in turn return to nature via a process of relatively rapid biodegradation. This is commonly termed ‘cradle to grave’ thinking and has permeated industrial design from office furniture to the automotive industry.
The second pathway involves utilizing pre-existing waste pathways to re-introduce waste products into new and innovative products. The ubiquitous ‘recycled bottle fleece’, for instance, has come to define this approach.
The third approach is designing products that can be used and maintained for as long as possible, minimizing the long-term environmental cost. This is the route that fine men’s footwear has, perhaps inadvertently, come to be associated with a more sustainable way of life.
Although unintentional, many of the processes in the making of fine footwear — such as oak bark tanning and the utilization of byproducts (raw-hides) from the meat industry — have some environmental benefits compared to more industrial manufacturing processes. Others, such as the glues and tanning chemicals used, are more inherently damaging.
The purpose of this article is to deconstruct the environmental cost of various components of men’s fine footwear. This way, we could more accurately assess the cost-benefits of investing in quality shoes from an environmental standpoint.
Given the vastness of the shoe industry, the multiplicity of manufacturing processes used, and the inability to address all environmental, social, and welfare concerns involved, this article merely seeks to be an introduction into the sustainability of men’s welted footwear and is in no way comprehensive.
This article will focus on three main components of shoes; the construction, the uppers leather, and other materials used, and what to expect at all three levels of investment.
Notably, this write-up and the following individual shoe style guides seek to present sustainable options that are both geographical and economically accessible to all. As such, it will present three levels of price: Attainable (below $400 USD), Advanced (400-800 USD), and Aspirational (over 800 USD).
These price brackets should indicate that good shoes are inherently costly, due to the quality materials and skilled workmanship required to craft them.
Construction
This is arguably the area that provides the greatest longevity to the shoe in practice. Whilst many forms of construction are used in footwear, this section will focus on four main methods that enable a relatively easy resoling of shoes.
Resoling is the easiest way to guarantee years of service from one’s footwear, and the ability to do so is central for true shoe sustainability. The methods investigated in the following all involve some combination of stitching and gluing the soles in place, ensuring a strong bond that will not fail in general use.
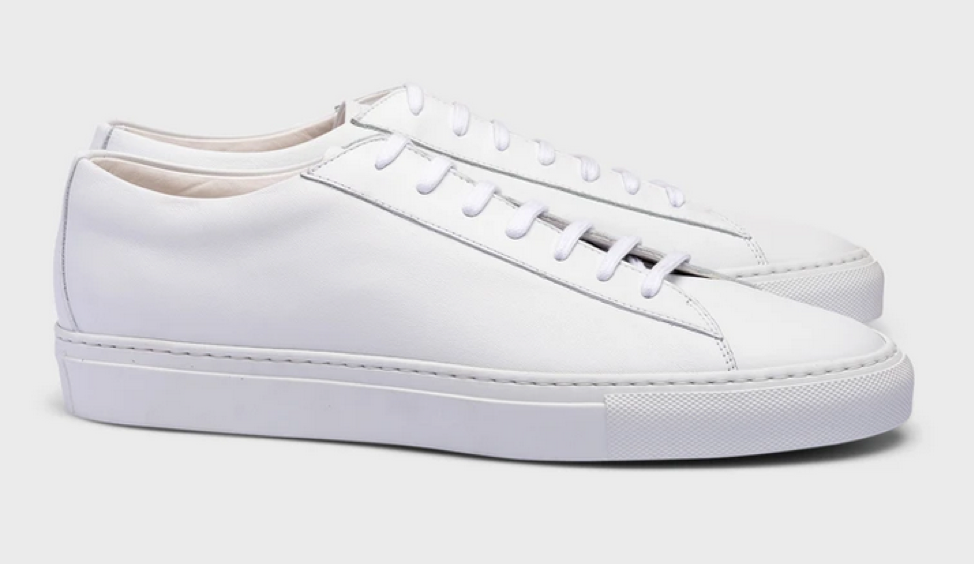
The first method is most commonly seen in very casual shoes such as sneakers and boat shoes. It is called a ‘cup-sole’ construction and involves a one-piece molded sole with high sidewalls that is glued (cemented) to the insole, and then stitched along the sides of the upper to ensure strength and durability.
As the uppers are simply pulled around the insole and glued in place, this provides a very low-profile shape to the shoe. The construction can have a thin layer of foam (such as Poron) or cork as a midsole, or none at all.
The best models utilize a thick leather insole similar to welted shoes, although many use a leather board or other composite material. The insoles used in a particular shoe have a large bearing on their long-term comfort and ability to take the shape of the wearer’s foot, and could be considered the ‘backbone of a shoe. Even in shoes with a cup-sole construction, look for the highest quality insole (sometimes also referred to as a lasting board) to ensure longevity.
While resoling cup-soled shoes is a relatively simple operation, many cobblers have little to no experience with the procedure. Look for a skilled repair person with the right materials on hand to carry out this task.
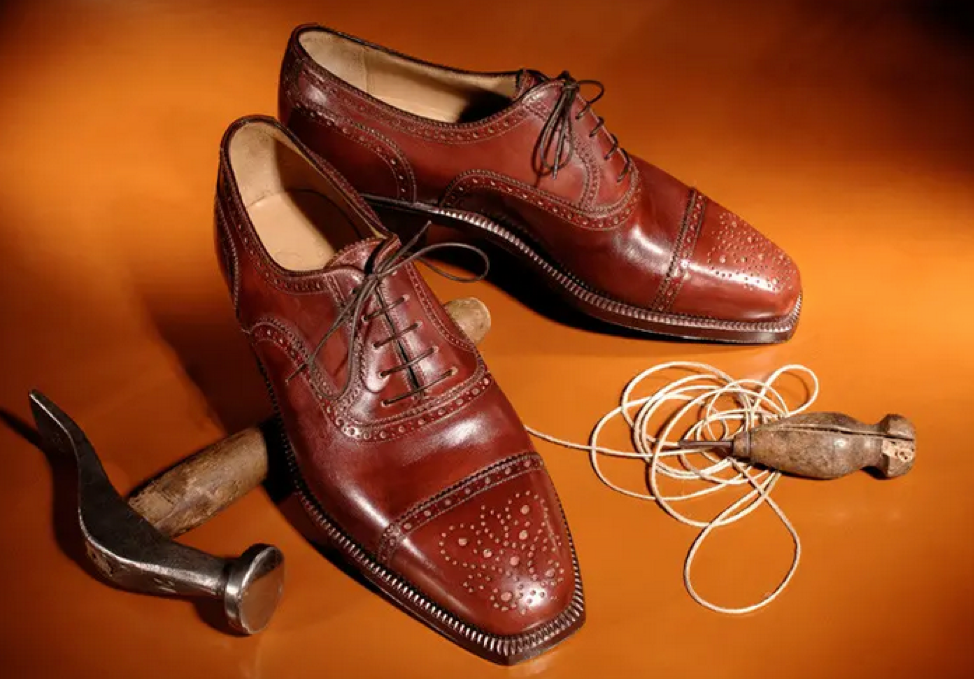
The second method that could be recommended for long-lasting shoes is the Blake-rapid construction. This differs from the more common Blake construction in several ways that allow both increased water protection and a more straightforward resoling process.
On the one hand, a standard Blake stitched shoe involves a specialized machine that stitches the outsole (typically leather) directly to the Insole. This allows for a very minimal profile, and immediate flexibility, but the stitch-holes in the sole allow water ingress. The machine needed to restitch the soles is also not commonly available to most cobblers.
Meanwhile, the Blake rapid process solves these issues by utilizing that outsole as a midsole and using the edges of that midsole as a welt of sorts. This allows the attachment of an outer sole similar to a Goodyear welted shoe, which allows easier replacement with an outsole stitching machine. The outsole also blocks any water migrating through the sole. Of course, the extra layer of leather slightly enlarges the sleek profile, but it is a small price to pay.
Another factor to consider is that in high-quality Blake-rapid stitched shoes, there will be three layers of leather underfoot; insole, midsole, and outsole. While these layers will naturally conform slightly to ones’ foot, they will not mold in the same manner as the thicker cork midsole found in the next two construction options.
This method of construction still holds merit in lighter Continental style loafers and summer shoes, but with the advent of very affordable Goodyear welted shoes, they lose traction somewhat in most other styles.
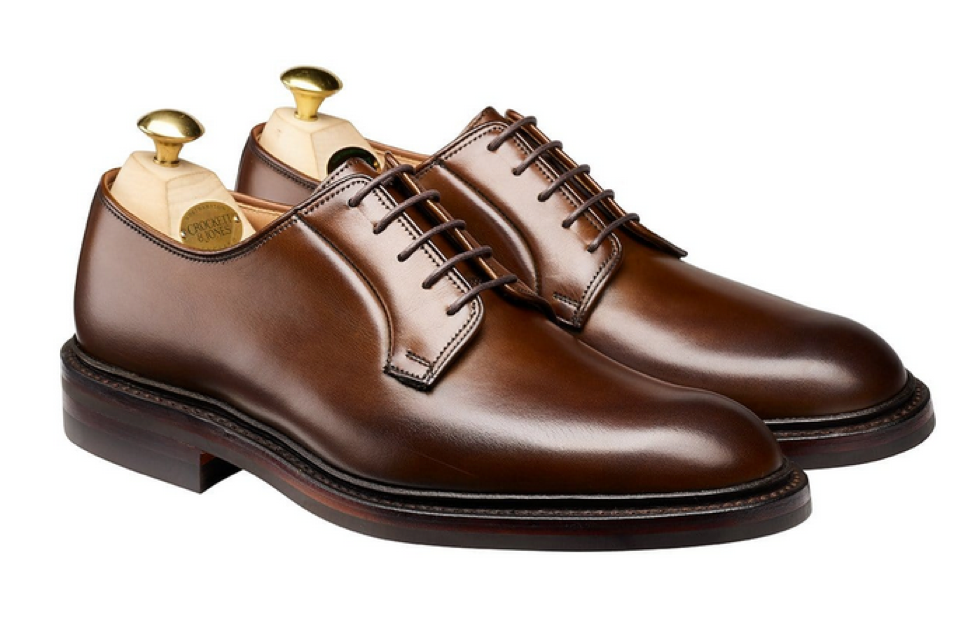
Goodyear welting has become something of a byword for quality in the men’s footwear space. While the construction method has some significant benefits in terms of comfort and longevity, it is not a silver bullet and does have some drawbacks, particularly at the more affordable level.
Contrary to popular belief, this method of welting was actually invented by August Destroy in 1862, rather than Charles Goodyear Jr. of Goodyear Tires fame. Like most stories of innovation go, Destroy’s invention was handily scooped up by the vulcanization mogul in a clever bit of market cornering. (One might imagine a possible reality where shoe lovers of the world swoon over the Destroy welt…)
The entirely mechanized process involves the gluing of a canvas rib — gemming — around the bottom of the insole, upon which the uppers and a thin strip of leather called a welt are stitched. The void on the bottom of the insole is filled with cork, and the outsole is stitched around the perimeter of the welt. Variations of welts are known as split, reverse or storm welts.
The welt itself can follow the entirety of the shoe’s perimeter (360-degree welt), or around the toe of the shoe from the base of the heel (270-degree welt). The outsole can easily be replaced, and the thick cork midsole provides a huge amount of comfort by allowing the leather insole to conform over time to the wearer’s foot. The fact that this process is entirely mechanized allows production at scale; and is, perhaps, the reason why it has become such a popular construction in recent years.
The welting can be replaced by competent cobblers, although the canvas rib could be seen as a potential source of weakness in the design. Only after decades of hard wear would this likely be a problem, but with particularly durable uppers like Cordovan, it could pose an issue. Shoes made with this method hold a certain visual (and actual) weight. At the affordable level, shoes made in this way can be challenging to break in due to the inflexibility of the more affordable, but less supple leathers used.

The final method of construction is likely only to be encountered at the highest levels of ready-to-wear footwear, although several enterprising brands are starting to introduce it into lower-priced made-to-order lines. We are, of course, speaking about hand-welting.
Prior to the mechanization of the Goodyear welting process, this was the main method for producing quality shoes; and remains the gold standard for construction methods. It is a highly skilled and laborious process that involves carving a thick leather insole to form a base to which the uppers and welt are hand-sewn onto, in essence taking the best features from both Blake Rapid and Goodyear welting.
The outsole is sewn in a similar fashion to Goodyear welting, although this is often done by hand, another very skilled and time-consuming operation. The result is a shoe that can be lasted (stretched onto its form) very precisely, finished beautifully, resoled easily, and has no discernable points of failure. Hand-welted shoes typically have tell-tale stitch indentations on the insole.
Moving on from hand-welting, various other methods of construction exist; including Veldschoen, Bolognese, Goyser, Norwegian, and many more. While these styles all have their own benefits, the differences are largely aesthetic as opposed to longevity-focused and are better covered in other online resources, such as the excellent guide at the Misiu Academy

Entry Level Goodyear-welted shoes (Photo from Meermin)
What to expect at the Affordable (less than $400 USD) level
Somewhat astoundingly, in today’s buyer-preferencing market, all of the aforementioned construction methods can be found in this price range, although with various concessions to quality.
For cup-sole constructed shoes, you should expect the highest quality possible; with Margom (or equivalent high-quality rubber) outsoles and fully leather insoles, cork filler and properly lasted uppers.
Blake Rapid shoes will be available from many brands — most likely with the exception of the designer category, however — and should have fully veg-tanned insoles with leather or rubber outsoles for longevity.
Goodyear welted shoes in this category are likely where one starts to see some corners having to be cut to meet the price. One should still expect a thick leather insole, robust canvas gemming, cork midsole, and full leather welt. It is possible for some manufacturers to produce shoes with high-end branded rubber or oak-bark tanned outsoles in this price range, but it is perhaps the exception to the rule.
Hand-welted shoes in this price range are a far trickier proposition. Brands manufacturing in East and Southeast Asia — with Meermin being a notable example — have been able to produce ranges with a hand-sewn welt, although they tend to have machine-stitched and finished soles. Also, be mindful that such a significant input cost might be compensated for elsewhere on the shoe, such as upper leather. In this price range, seeking the highest quality uppers is the priority over handwork.
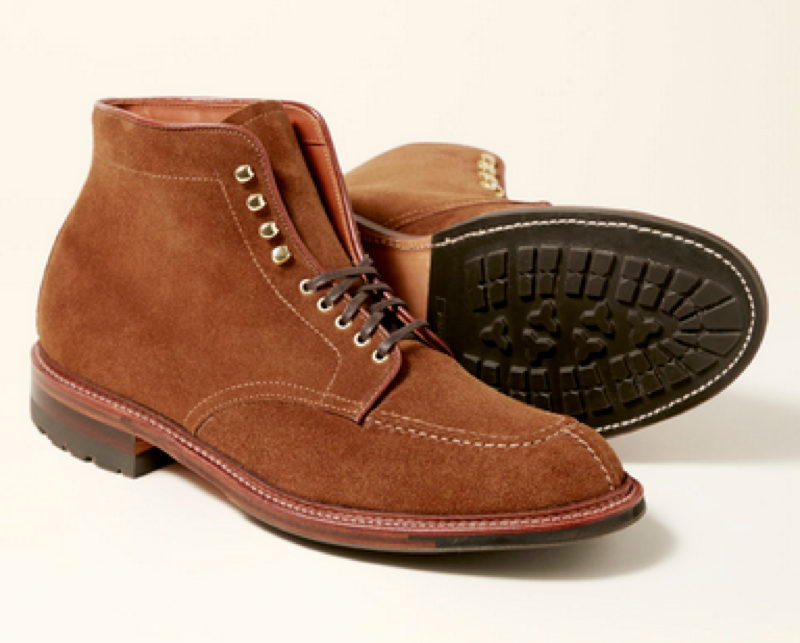
What to expect at the Advanced ($400 -$800 USD) level
One should be seeking very fine Goodyear welted or more basic hand-welted footwear. While it is possible to find cup-soled and Blake rapid construction shoes, these are mainly found on shoes whose primary attraction is the brand name on the box.
Here the most respected Goodyear welted shoes can be found, with many variations of full leather welt, thick buffed veg-tanned insoles, and Oak-Bark tanned or Dainite branded outsoles. Some manufacturers, such as Alden, even include a more sturdy ‘triple rib shank’ and canvas reinforcement for the gemming. Again though, these may reflect deficiencies of make in other areas. Look for fully leather heel counters, stacks, and natural shank materials at this level.
Hand-welted shoes also start to get interesting at this level. Several manufacturers, largely from Italy, Hungary, and Spain, have very interesting shoes in this price range. High-quality uppers, hand-welted over attractive lasts, and usually machine stitched to quality outsoles — this is the domain of the true aficionado. Although as with many things, it is very easy for prices to escalate quickly into the next price range. Look for all of the same features as with Goodyear welted at this price.

What to expect at the Aspirational (Over $800 USD) level
Here, artistry eclipses function, as all of the benefits of Goodyear and hand welting have been reached.
Some manufacturers, such as Gaziano and Girling, step up the quality of materials to their zenith by using J&FJ Baker insoles, outsoles, and counters. Others use the inherent benefits of the hand-welting process to beautify the shoes to the highest degree.
While it can be argued that the shoes available in this price range do not necessarily have an inherently longer life than others purely from a construction perspective, as will be examined shortly, construction only forms a part of a finished shoe.
Upper Leather
Undoubtedly, upper leathers constitute a significant cost of the final shoe, as customers ordering custom uppers in a made-to-order program can no doubt attest.
Manufacturers pride themselves on the materials used in uppers, and will often advertise the tannery used, particularly in the affordable range. If a manufacturer utilizes hides from established European tanneries, you can be reasonably assured that the leather is produced in an environmentally conscious way due to the tight legislation that governs this industry. It always pays for the end consumer to investigate the leather used to ensure respectable tannery practices, but generally, buying higher-end footwear ensures a quality tannery.
Most leathers used for high-quality shoes are sourced from Western-European tanneries, traditionally French, Italian, and German. There remain several English and American tanneries, and some rising stars in Japan.

Changes to European legislation over the years have caused the closure or movement of even the most famous tanneries producing high-quality upper leathers. The German Freudenberg tannery is one such prominent example, with the tannery moving to Poland and changing its name to Weinheimer. This was largely due to the tightening of environmental standards surrounding the aniline dying process of box calf, for which the tannery was famous.
Upper leathers made using these aniline-dyed, chrome-tanned processes do have a wonderful smoothness and luster but are perhaps one of the most chemically-intensive leathers to produce. (Something to keep in mind for fans of Black cap-toe Oxfords…)
This said, most well-known tanneries used in high-end footwear have closed-loop environmental waste systems that process contaminants out of the wastewater before returning it to the source.
Tanning — especially the vegetable variant — is an inherently water-intensive process, and most traditional tanneries were located alongside rivers for this reason. Some, such as the esteemed J&FJ Baker tannery in Devon, still use the river to power the tanning process via a 400-year-old water wheel mechanism.

Suede typically follows the same processes as chrome-tanned upper leathers, but is then split and sanded, then re-tanned. Notably, even the highest quality suedes use this process; and this is, therefore, one reason why there may be a cost-benefit argument for minimizing expenditure on suede footwear.
In several very high-end suedes known as reversed calf suede, the full-grain is maintained intact on the inner side of the skin. A famous version of this is the aptly-named Janus suede by famous British Tannery C.F. Stead. This full-grain profile is similar to the heavier ‘roughout’ leathers used in some work boots.
Elsewhere, the carbon miles for any leather upper should also be a consideration. It is not uncommon for a hide to travel from a tannery in the USA, to be manufactured in Spain, and then sent to a store in Hong Kong, only to be then purchased by an internet shopper in Australia.
A globalized world brings enormous possibilities for the savvy web surfer but has hidden consequences for the composition of the atmosphere. It can be extremely challenging to find a shoe constructed from totally local materials until one reaches the upper echelons of the bespoke process.

Finally, although we hope that our footwear can last our lifetime, sometimes shoe uppers are just too worn out to be used further. In this case, it is important to dispose of shoes in a mindful way.
For instance, the trivalent chromium used in tanning uppers leather can become the hazardous Hexavalent Chromium when burned, and as such, all shoes should be disposed of into a waste stream that eliminates the possibility of burning.
The best disposal option would be to visit the local cobbler, as they typically have methods of collecting waste leather for reprocessing into ‘leather-board’ (think leather cardboard) or similar composite materials.
(For a fantastic discussion of the relative environmental benefits of the leather tanning process, see Jesper Ingevaldsson’s interview with Jacques Kress of Tannerie Haas on the Shoegazing podcast.)

Du Puy's famous country grain (Photo from Skolyx)
What to expect at the Affordable (less than $400 USD) level
Young, up-and-coming footwear producers are the first to shout about the leather used in the uppers of their shoes and boots. Famous Tanneries such as Horween, Annonay, Weinheimer, and C.F. Stead are used for their associations with higher-end brands.
What really makes the difference, however, is both the quality of the leather used and how the hide is clicked (cut) to avoid defects. Even the best, most renowned tanneries produce a range of qualities from unblemished first grade, to less perfect second grade and more. The more established brands have access to the best hides first - although often after luxury handbag makers - with more of the second-grade skins going to more accessible makers.
Then, as a consequence of the need to utilize more of the hide, the skins are clicked less selectively (maybe 4-5 shoes per hide), and may include more natural blemishes. That is not to say that these shoes will last any less time, rather that they may not be aesthetically perfect.
This is when suedes and grain de-bossed leathers are at their most useful in producing high-quality footwear at a reasonable price point. Look for Tanneries Du Puy's country grain and CF Stead’s Repello suede for a fantastic value in this segment. Some of the aniline-dyed box black calfskin, such as Weinheimer can be quite consistent at this level too.

What to expect at the Advanced ($400 -$800 USD) level
This is the level at which consistently flaw-free uppers from established tanneries might be expected. Burnishable calf leathers such as Haas’s Nevada, stunning crust leathers such as Annonay’s Vegano, and Ilcea’s famous museum calf leathers are at their best here.
Coupled with the availability provided to more established manufacturers at this level, the hides are more heavily scrutinized, with maybe only two or three shoes being taken from a hide. While the aesthetic beauty of the hides will increase in quality, the thicker grain and suede leathers might still be more resilient over the long term.
Fully vegetable-tanned upper leathers are more commonly found at this level, and this might appeal to those with concerns over the chrome tanning process. Even white, highly finished leathers for sneakers, which were traditionally only chrome-tanned, can now be found with metal-free tannage from brands like Vekla. It is still relatively uncommon to find full-grain suede leathers (reverse calf) in this price range, nevertheless.

What to expect at the Aspirational (Over $800 USD) level
Here, one could start to encounter a whole number of exotic and unique leathers. This article will not attempt to deconstruct the many conundrums of exotic leathers, and will only explore terrestrial, herbivorous mammals that are not bred for their skins.
Kudu, reindeer, kangaroo, cordovan (horse rump membrane), and sheep (shearling) all have a long history of use in leather; and many environmentalists actually prefer the fact that many of these animals are typically not bred in captivity.
They may offer some unique benefits including incredible resilience (cordovan), warmth (shearling), increased flexibility (kangaroo), surface texture (kudu), or unique historical interest (Russian reindeer leather). They typically also command a higher premium due to their wild-harvested nature and may display more signs of a life lived in the natural environment.
Of course, in this price range, one has the pick of the best calf leathers and can sample the velvety softness of a full-grain suede from even the most prestigious tanneries.
Other Materials
Although the upper leathers constitute a large percentage of the overall cost of a shoe — from an environmental perspective — all of the other materials of a shoe, such as lining leathers, glues, toe, and heel reinforcements, and sole materials all bear a significant environmental cost.
Lining leathers are typically made from vegetable-tanned leathers. The reason for this is simple — many of the residual chromium salts from the chrome-tanning process can contact an individual’s skin and cause horrific allergic reactions. In other words, at all levels of footwear recommended, you should expect a completely vegetable-tanned lining leather.
Some exceptions may apply here, however, as the lining leathers may be a calfskin or a kidskin at times. Notably, kidskin is thinner, slightly more flexible, and is generally considered an upgrade over calfskin. Additionally, these lining leathers are typically undyed. However, some manufacturers will dye the leathers for an additional aesthetic component. That being said, you should remember there is always an environmental cost to this.
Unlined shoes can be found for summer wear, although one must be mindful that these uppers (often suede) are likely to be chrome-tanned and should not be worn sans socks for risk of skin irritation. (See Sean Gallagher’s brilliant photo essay on the human cost of low-priced chrome-tanned leather, and for evidence of why to keep it from your skin.)

Glues are a common component in all shoes for attaching the lining to the upper, the upper to the welt, and the sole to the welt.
In most shoes, the glue used will be cohesive (as opposed to adhesive) that works by both surfaces being glued and re-activated in turn. The glues are relatively benign to the end consumer, although many use organic solvents that can be harmful to workers with continued exposure.
At the upper levels of shoemaking, it is more common to encounter the glue Hirschkleber. This natural product is made with potato starch and is used to glue parts of the uppers in high-end shoes. It has the benefits of being highly breathable for the end-user and does not produce fumes in use.
Toe and heel reinforcements are necessary for leather shoes to maintain the shape of the last for many years, and can be a key component to ensure comfort and longevity in a shoe.
At the more industrial end, it is common for shoe manufacturers to use a thermoplastic heel and toe stiffener, which are easily formed onto the last and require minimal shaping. These can provide a decent fit if the last suits the wearer, but cannot mold to the user’s foot over time. This is less of an issue in the toe stiffener (counter) than the heel, as repeated stress on the heel is more common, and can lead to the internal disintegration of the counter over time.
The next step up typically involves keeping the thermoplastic toe counter, though using either a leather-board or full leather heel counter. While both will provide the custom molded shape over time, the full leather will do so with greater longevity and breathability.
At the highest levels of footwear, you may see full leather heel and toe counters, which will be highly breathable and resistant to wear. The time needed to shape, harden and trim these pieces can be significant.
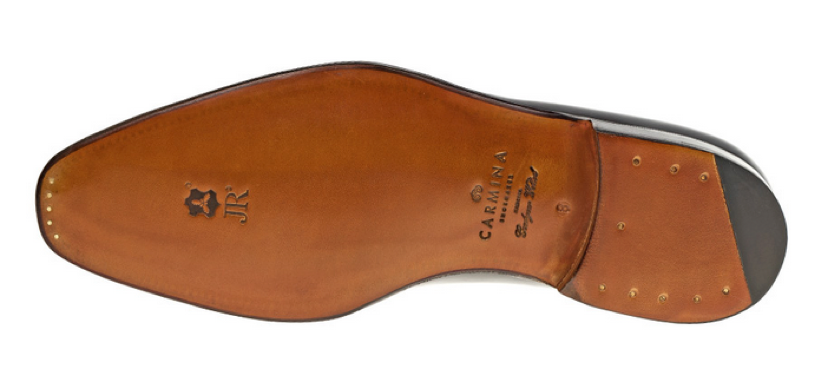
Sole materials can range from natural crepe, to oak-bark tanned leather, to Dainite rubber soles. All materials have benefits and drawbacks both from a wearability and sustainability perspective. Here, we will focus on the typical sole materials of leather (single and double) and rubber (natural and synthetic).
Leather soles are the most traditional and elegant style of soles. They are typically associated with business oxfords, lightweight summer loafers, and are often stacked double on sturdy country brogues. Highly regarded producers of this leather include Joh Rendenbach, Garat, and J&FJ Baker. All utilize local sources of plant tannin, such as English Oak, Chestnut, and Willow.
Notably, the process used to create the tight fiber structure of a highly wear-resistant sole leather demands a long curing time in a bath of vegetable tannins. While this process may be slow, it is inherently low-impact. There is one caveat, however. It demands large quantities of fresh water.
The time invested in these processes necessitates a higher cost. The quality of soling leather is often higher in Spanish and Italian makes, as compared to English and US manufacturers, at least in the affordable range. While leather soles provide unequaled breathability, flexibility, and comfort, they can be very slippery in wet conditions and will need replacement sooner than rubber, with all else being equal.

Rubber soles have been experiencing a wave of popularity recently, with many manufacturers offering new models on Vibram, Dainite, or even crepe soles.
This is invariably due to the increased grip and longevity provided by high-end rubber soles. It is unsurprising, therefore, that manufacturers have made great strides in recent years to develop rubber soles that appear sleeker in profile, which will work in a more formal setting.
When it comes to rubber soles, the most ‘natural’ version is the crepe sole. A coagulated latex in essence, this sole material gained popularity alongside the ‘desert boot’, where its comfort and lightweight suited the desert environs of North Africa. This material, however, is far less suited to the city. It attracts dirt, wears down quickly on hard surfaces, and is very slippery in wet weather conditions.
A far better option is one of the many modern synthetic rubber offerings from Vibram or Dainite. Although being synthetic products themselves, the durability and grip offered by these soles are unmatched. Moreover, they also come in a myriad of colors, lug patterns, and sizes. At the affordable end, many manufacturers are producing their own ‘studded soles’ that mimic the performance characteristics of the more well-known products.
Both rubber and leather soles have a place in the modern man’s wardrobe. City oxfords and lightweight loafers demand high-quality single leather (or thin modern rubber) soles, whereas chunky boots and country shoes would better suit a Dainite sole. Less easy to recommend are double leather soles or fragile crepe rubber soles. This is an area one should carefully examine where a pair of shoes is worn, and what soling material best suits that purpose.
In a careful rotation, both types of soles should last at least one year of wear before needing replacement, and in many cases far more. Carefully consider the need to replace the welt along with the sole, as doing so can shorten the life of your shoe. Some manufacturers include this service as standard in a factory refurbishment, so caveat emptor.

What to expect at the Affordable (less than $400 USD) level
Expect fully vegetable-tanned lining leathers, especially if the shoes in question are likely to be worn sans chaussettes in summer. Although many ‘high-end’ brands utilize cotton or linen fabric linings at this price range and higher, the longevity and comfort offered by a full leather lining cannot be overstated. Glues will invariably be chemical-based, but again, a fully stitched veg-tanned leather lining will eliminate the possibility of your skin meeting any glue.
Heel and toe counters (or puffs in the US) will likely be thermoplastic. Many brands are starting to differentiate themselves by offering leather-board or real leather heel counters, and this is a real step up in comfort and longevity, take heed. Below the level of hand-welted shoes, leather toe counters make a marginal difference to comfort.
Soles will typically be a non-Oak bark tanned single leather or a non-branded studded rubber sole. These both work well, although they will not provide quite the lifespan of the more expensive options. Upon resoling, these can both be upgraded, although doing so will add a touch of visual weight to the soles. For cup-soled shoes, you should expect the highest quality Margom outsoles, or the equivalent thereof.
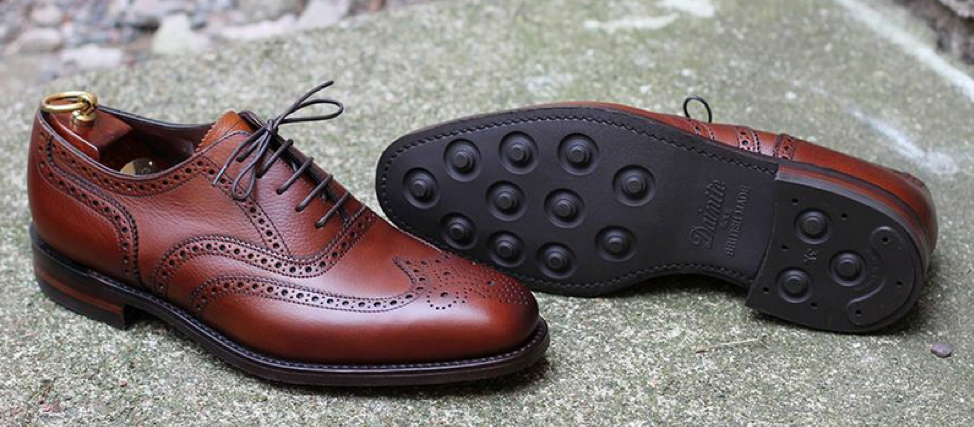
What to expect at the Advanced ($400 -$800 USD) level
Stepping up sees some general improvements in all areas. Lining leathers may be slightly softer and more supple, and finished with a higher degree of care. Heel counters should be real leather, even if the toe counter is still likely thermoplastic.
Glues may also be less toxic. This is largely governed by the location of the factory, with certain countries (particularly within the EU) having quite tight environmental restrictions regarding solvents. This is also something that very few manufacturers advertise.
Another less visible, but still very tangible upgrade is an increase in the quality of the leather used for the insole. Considering it forms the ‘backbone’ of the shoe — and is where one’s foot rests on the shoe, after all — the use of a slightly thicker, buffed leather insole can markedly increase the comfort of a shoe.
For soles, expect high-quality oak-bark tanned leather or lugged/studded rubber outsoles from the likes of Vibram or Dainite. While some manufacturers still supply shoes with lower quality soling materials at this price, the quality of the leather used for the uppers demands that a similar approach be taken for the soles.
As the soles are replaced time and again, the welt will degrade, wearing out at a faster rate than the uppers. This requires a very expensive trip to a skilled cobbler to re-welt the shoes. A far better option is to upgrade the sole material to match the longevity of the uppers. (An interesting discussion of this conundrum can be found at the fantastic Shoegazing blog under the Guide to resoling and re-heeling.)

Beautiful Gaziano & Girling soles (Photo from Skoaktiebolaget)
What to expect at the Aspirational (Over $800 USD) level
The pinnacle of shoe materials can be found here, with thick, oak-bark tanned insoles, hand welted to equally thick and robust outsoles of the same material.
Toe counters and heels are often leather, but not always. The toe-lasting machines that produce factory-made Goodyear welted shoes — even to the highest level — will still utilize a thermoplastic toe counter. Hand-welted shoes may have either, though they really deserve leather.
The glue used on these natural counters is the aforementioned Hirschkleber, which allows further breathability and comfort. Veg-tanned leather linings are a given, as are the highest-grade outsoles in leather or rubber.
Many manufacturers actually deviate from the name-brand soling materials in this range, offering half leather, half rubber soles replete with protective toe taps, and decorative nail designs from the factory. It goes without saying that the level of finishing to these materials goes beyond ‘production’ into ‘artistry’, and this may be worth the price of admission for many.
Conclusion
In the early 1960s, American economist Walt Whitman Rowse created a theoretical framework for the progression of a societies’ economy that continues to be referenced today. He created five ‘stages’ of economic development encompassing the forces of industrialization, diversification, and internationalization leading a country from ‘Traditional society’ to ‘The era of mass consumption'.
Revising his work in 1971, he predicted a sixth age, which he termed ‘The search for quality’. In such an age, he envisaged consumers rejecting the idea of continued mass consumption in preference for a lower number of durable and traditionally made goods. It could be argued that in many developed societies, such an age is currently underway.
The dual pressures of the environment and economy have led many individuals to seek timeless, high-quality/ value goods that might better serve them in the world to come. Thus, it is the authors’ hope that quality menswear plays a defining role in such a paradigm change, and that intentional consumption can help to slow some of the changes occurring to our planet.
It is in this vein that the following series suggests some time-honored styles and quality manufacturers that may provide such a future-proof footwear wardrobe.
Photography: as stated, otherwise own
Hi, thanks for your detailed answer, looking forward to read the future articles !
Hi, so reading your article I understand going over 800$ doesn't bring any longevity benefit to shoes. But do shoes in the 400-800$ bracket have twice the lifespan than those under 400$?